Produkte
Suchen
3D-MID
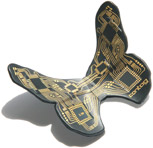
Diese Zusammenführung der Funktionalitäten erschließt völlig neuartige Möglichkeiten in der Systementwicklung. Damit ergänzt sich das Portfolio der alternativen 3D- bzw. 2,5D-Techno-logien wie flexible und verformbare Leiterplatten um Möglichkeiten, die im Gesamtsystem nur durch MID technologisch sinnvoll und kosten-günstig realisierbar sind. Hier bietet 3D-MID die intelligente und elegante Lösung der Systementwicklung.
CONTAG bietet von der Beratung beim Design und der Auswahl eines geeigneten Materials über das Rapid-Prototyping bis hin zur Serienfertigung und Bestückung einen umfassenden Service für 3D-MID-Projekte an.
Material und Herstellungsverfahren
Designregeln
Bestückung und Weiterverarbeitung
Anwendungsbeispiele
Zusammenfassung und Ausblick
DOWNLOAD Produkt-Info 3D-MID
Material und Herstellungsverfahren
a) Rapid-Prototyping
Prototypen und Funktionsmodelle
Mit dem Rapid-Prototyping können innerhalb kurzer Zeit und für ein überschaubares Budget 3D-MIDPrototypen und Funktionsmodelle hergestellt werden. Die Validierung des Designs und der Funktionalität gibt vor der Investition in die Serienproduktion die Sicherheit für den Erfolg eines Projekts. Hierbei setzt CONTAG auf den 3D-Druck in Kombination mit der Laserdirektstrukturierung (LDS). Bei niedrigen Stückzahlen kommt das Rapid-Prototyping auch für Endanwendungen infrage.
CONTAG bietet dabei als ein mögliches Verfahren den Stereolithographie-3D-Druck (SLA) bis zu einer Größe von 145mm x 145mm x 175mm an. Im Vergleich zu anderen 3D-Druckverfahren zeichnet sich das SLA-Verfahren durch eine hervorragende Oberflächenbeschaffenheit und Detailtreue aus. Das Funktionsprinzip basiert auf dem schichtweisen Aushärten eines flüssigen Harzes mithilfe eines UV-Lasers. Dabei beträgt die
minimale Schichtdicke 0,025mm. So entstehen aus CAD-Daten qualitativ hochwertige Grundkörper für 3D-MID-Prototypen. Mit dem HighTemp-Material steht dabei eine Variante zur Verfügung, welche den thermischen Anforderungen von Reflow-Lötverfahren und auch zahlreicher Endanwendungen gerecht wird. Darüber hinaus spricht die chemische Stabilität der SLA-Materialien für sich. Sie sind chemisch beständig gegenüber Laugen, Säuren, (Mineral-)Ölen, Fetten, Kohlenwasserstoffen, Salzwasser, und Wasserstoffperoxid.
Eigenschaft | Standard-Material | Hoch-Temperatur-Material |
---|---|---|
Erweichungsbereich | 73,1°C | 289°C |
Bruchspannung | 65 MPa | 51,1 MPa |
Bruchdehnung | 6,2% | 2% |
Kennwerte der Stereolithographie-Materialien
Nach dem 3D-Druck wird die Oberfläche des Grundkörpers mit dem Speziallack ProtoPaint beschichtet, welcher speziell für die Laser-Strukturierung (LDS-Verfahren) entwickelt wurde (siehe unten). Durch strukturierte Laserbestrahlung wird der Lack entsprechend des Layouts aktiviert und anschließend metallisiert. Layoutstrukturen bis zu 200μm line/space können auf diese Weise realisiert werden. Der glänzend schwarze Lack zeichnet sich durch hohe Haftfestigkeit sowie Thermostabilität aus und verleiht Ihrem Produkt darüber
hinaus auch einen edlen Charakter.
b) Klein- und Großserienfertigung
Für die Serienfertigung von 3D-MID gibt es verschiedene etablierte Verfahren, die CONTAG beide beherrscht und
anbietet.
- 2-Komponenten-Spritzguss
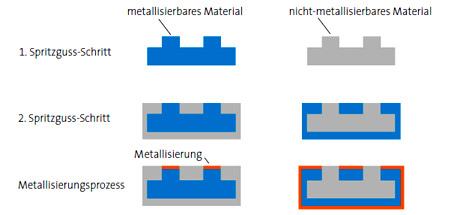
- 1k-Spritzguss und LDS-Verfahren
- 1k-Spritzguss auf Basis gefräster Aluminium-Werkzeuge
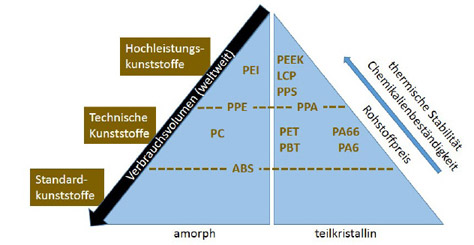
c) Weitere Materialien
Prinzipiell sind auch Duroplaste für 3D-MID-Anwendungen geeignet. Im Gegensatz zur Leiterplattentechnologie spielen Duroplaste für 3D-MID bisher aber eine untergeordnete Rolle. Die Thermoplaste, insbesondere die Hochleistungskunststoffe, werden den Anforderungen in den meisten Anwendungsfeldern gerecht. Darüber hinaus sind Thermoplaste aufgrund ihrer Thermoverformbarkeit einfacher zu verarbeiten als Duroplaste.
Weit verbreitete Vertreter von 3D-MID-Hochleistungs-Thermoplasten sind LCP-Materialien (liquid crystal polymer). Diese teilkristallinen Kunststoff-Compounds enthalten einen hohen Grad an Füllstoffen und zeichnen sich durch hervorragende thermische und elektrische Eigenschaften sowie sehr gute Chemikalienbeständigkeit aus.
Eigenschaft | Wert |
---|---|
Dichte | 1,76 g/cm3 |
Erweichungsbereich | 277 °C |
Bruchspannung | 165 MPa |
Thermische Ausdehnung | x:16 / y:32 ppm/K |
Feuchteaufnahme | < 0,1 % |
Wärmeleitfähigkeit (senkrecht || parallel) | 0,76 W/m*K || 1,61 W/m*K |
Dielektrizitätskonstante εr | 3,8 (1 MHz) |
Verlustfaktor tanδ | ca. 0,03 (1 MHz) |
Durchschlagsfestigkeit | > 7,5 kV/100 μm |
Physikalische und elektrische Eigenschaften eines LCP-Materials von RTP
Weitere allgemeine Eigenschaften:
- Chemisch stabil gegenüber Ölen, Ozon, Teer, viele Lösemittel und verdünnte Säuren
- Hohe UV- und Witterungsbeständigkeit
- Realisierbarkeit von Durchkontaktierungen im additiven LDS-Verfahren
d) Laserdirektstrukturierung und Metallisierung
Die Laserdirektstrukturierung (LDS) kann in Additiv- und Subtraktiv-Verfahren unterteilt werden. Beim additiven LDS-Verfahren kommen Spritzguss-Rohmaterialien infrage, in die ein metallhaltiges Additiv beigemengt ist. Alternativ kann ein solches Additiv mit dem Protopaint-Speziallack auf die Oberfläche eines beliebigen Grundkörpers appliziert werden (siehe oben). Die Metallkeime werden durch die strukturierte Belichtung mit einem Laser entlang des elektrischen Layouts für eine chemische Metallisierung aktiviert.
Außerdem wird die Kunststoffoberfläche an den belichteten Stellen angeraut. Hier kann nun chemisch 5-10μm Kupfer abgeschieden und anschließend z.B. mit dem bewährten ENIG-Prozess veredelt werden. Für die meisten Anwendungen ist die chemisch abgeschiedene Cu-Dicke völlig ausreichend, bei entsprechender Planung des Layouts im Vorfeld besteht aber auch die Möglichkeit der galvanischen Nachverstärkung. Die erreichte Haftfestigkeit bzw. Abzugskraft der chemisch abgeschiedenen Kupferbahnen liegt je nach Material im Bereich von 1,4N/mm und damit höher als in der relevanten IPC-Leiterplattennorm gefordert (>1N/mm).
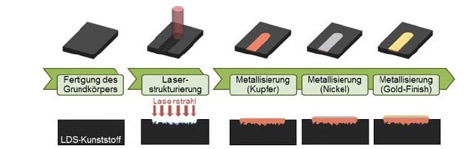
Beim subtraktiven LDS-Verfahren geht man von einem vollflächig mit Kupfer beschichteten Formteil aus. Auf die Oberfläche dieses Formteils wird ein Ätzresist aufgetragen und mit dem Laser strukturiert. Anschließend wird die freigelegte Kupferfläche weggeätzt und der Resist wieder abgetragen.
CONTAG bietet sowohl das additive als auch das subtraktive LDS-Verfahren an. Je nach Design und gewünschter Kupferbelegung empfiehlt sich die eine oder andere Variante.
Designregeln
Das elektrische Layout ist standardmäßig einlagig, aber auch doppelseitige und durchkontaktierte Schaltungen können realisiert werden. Dabei stellen sowohl das LDS-Verfahren als auch der 1kbeziehungsweise 2k-Spritzgussprozess sowie nachgelagerte Metallisierungs- und Bestückungsprozesse bestimmte Anforderungen an das Design des Grundkörpers sowie die Layoutgestaltung. Diese Anforderungen sollten schon in der frühen Entwicklungsphase Ihres Projektes berücksichtigt werden.
Beim LDS-Verfahren ist es beispielsweise notwendig, dass der Laserspot möglichst senkrecht in alle Bereiche entlang des elektrischen Layouts auf den Grundkörper auftreffen kann. Wenn der Grundkörper aus einem LDS-fähigen Thermoplast gefertigt wird, sollten scharfe Kanten mit einem großen Radius abgerundet sein, um durch Werkzeug-Rückstände verursachte Fremdabscheidungen zu vermeiden. Anderenfalls könnte ein zusätzlicher Vortauchprozess notwendig sein, wodurch die Oberfläche des Grundkörpers angeraut und die realisierbare Strukturauflösung auf 200μm line/space herabgesetzt wird.
Etwaigen Komplikationen durch thermische Beanspruchung und Lotabfluss sollte schon bei der Layoutgestaltung entgegen gewirkt werden. Zur Stressreduktion bei Temperatur-belastung ist es vorteilhaft, scharfkantige Richtungswechsel der Leiterbahnen zu vermeiden und die Ecken von Pads abzurunden. Auf die Verwendung eines Lötstopplackes kann oftmals verzichtet werden. Allerdings sind die Übergänge von Pad und Leiterbahn gleitend zu gestalten, so dass durch den Kapillareffekt ein Abfließen der Lotpaste verhindert wird. Auch das Ausdehnungsverhalten und die maximale Größe der Bauteile sollte mit dem CTE-Wert des verwendeten Thermoplasten abgeglichen werden, um einen allzu großen Versatz zu den Lötkontakten auszuschließen.

Die hier beschriebenen Empfehlungen sind nur eine Auswahl der wichtigsten Design-Regeln bei der Fertigung von 3D-MID. Für weitere Informationen setzen Sie sich möglichst frühzeitig mit dem CONTAG-Team in Verbindung. Ihre technologische Aufgabenstellung wird dann geprüft und mit Ihnen gemeinsam die für Sie optimale 3D-MID-Lösung erarbeitet.
Prototypen / Kleinstserien | Klein- und Großserien | Sehr hohe Stückzahlen | |
---|---|---|---|
Fertigungstechnologie | 3D-Druck (SLA) + ProtoPaint + LDS (additiv) | 1k-Spritzguss + LDS (additiv und subtraktiv) | 2k-Spritzguss |
Materialien | UV-aushärtende Harze | ABS, PA, PBT, PC, LCP, PEEK, u.v.m. | LCP/LCP, LCP/SPS, PBT/ PBT, u.v.m. |
Min. Leiterbreite/- abstand (mind. Ø Bohrloch) | 200μm/200μm | 100μm/100μm | 200μm/200μm (400μm) |
Vorteile | niedrige Initialkosten, kurze Lieferzeit, hohe Flexibilität im Grundkörper- und Layoutdesign | Materialvielfalt, hohe Flexibilität im Layout, hohe Strukturauflösung | verkürzter Metallisierungsprozess, günstig bei hohen Stückzahlen |
Nachteile | eingeschränkte mechanische Stabilität und Strukturauflösung | eingeschränkte Flexibilität des Grundkörpers | hohe Initialkosten, lange Lieferzeit, eingeschränkte Flexibilität und Strukturauflösung |
Übersicht der 3D-MID Fertigungstechnologien bei CONTAG
Bestückung und Weiterverarbeitung
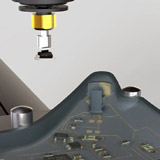
Falls die Verwendung von Lötstopplack notwendig ist, gibt es hierfür zwei Möglichkeiten. Einerseits kann vor dem Auftrag von Lotpaste selektiv an empfindlichen Stellen Lötstopp durch einen separaten Bearbeitungskopf des Bestückungsautomaten aufgetragen werden. Alternativ wird der gesamte Grundkörper mit Lötstopplack beschichtet. In einem anschließenden Laserprozess werden die zu lötenden Padflächen wieder freigelegt.
Zum Löten der vormontierten Bauteile können bei Grundkörpern aus Hochtemperatur-Thermoplasten gängige Reflow-Lötverfahren genutzt werden. Bei thermisch sensitiven Substraten kommen das selektive Laser-Löten oder andere Lötverfahren mit niedrigschmelzendem Lot infrage.
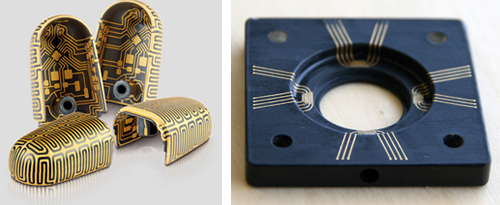
Zusammenfassung und Ausblick
CONTAG besitzt ein umfangreiches Know How und bietet von der Beratung in der initialen Planungsphase über das Rapid-Prototyping bis zur Fertigung von Klein- und Großserien ein komfortables Komplettangebot für Ihr 3D-MID-Projekt. Unser Antrieb ist die hochwertige Lösung für Ihre technologischen Herausforderungen. Bei Aufgabenstellungen, wo herkömmliche Leiterplattentechnologien an die Grenzen stoßen, ist CONTAG ein zuverlässiger und kompetenter Partner. Dabei wird aus einem umfangreichen Technologie-Pool geschöpft, um passgenaue Lösungen zu erarbeiten.
Für weitergehende technologische Fragen rund um das Thema „3D-MID“ wenden Sie sich bitte an unser CONTAG-Team (Tel. 030/351 788 -300 oder team@contag.de).
Ausgabestand: C